1.Continuous Auger Flight Machine
HY series Semi-active spiral blade cold rolling machine are the second generation Semi-active Spiral Blade Cold Rolling Mill products,which researched and developed by our company’s practical experience.
HY series of products are the advanced equipment for producing spiral blade ,which use the strip steel as the raw material and make continuous rolling operation. Compared with conventional cold forming practices which is used current widely, it just needs do some simple adjustments on the equipment’s adjustable parts (don’t need replace parts), like the device dials and pressure gauges, and then roll out various kinds of spiral blades required. This series of products have the advantages of flexibility to adjust the production specification, high efficiency production, saving raw materials, high leaf hardness and good wear resistance.
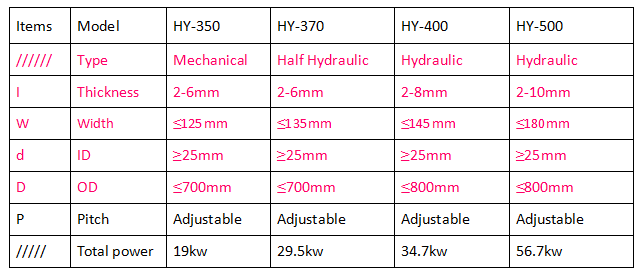
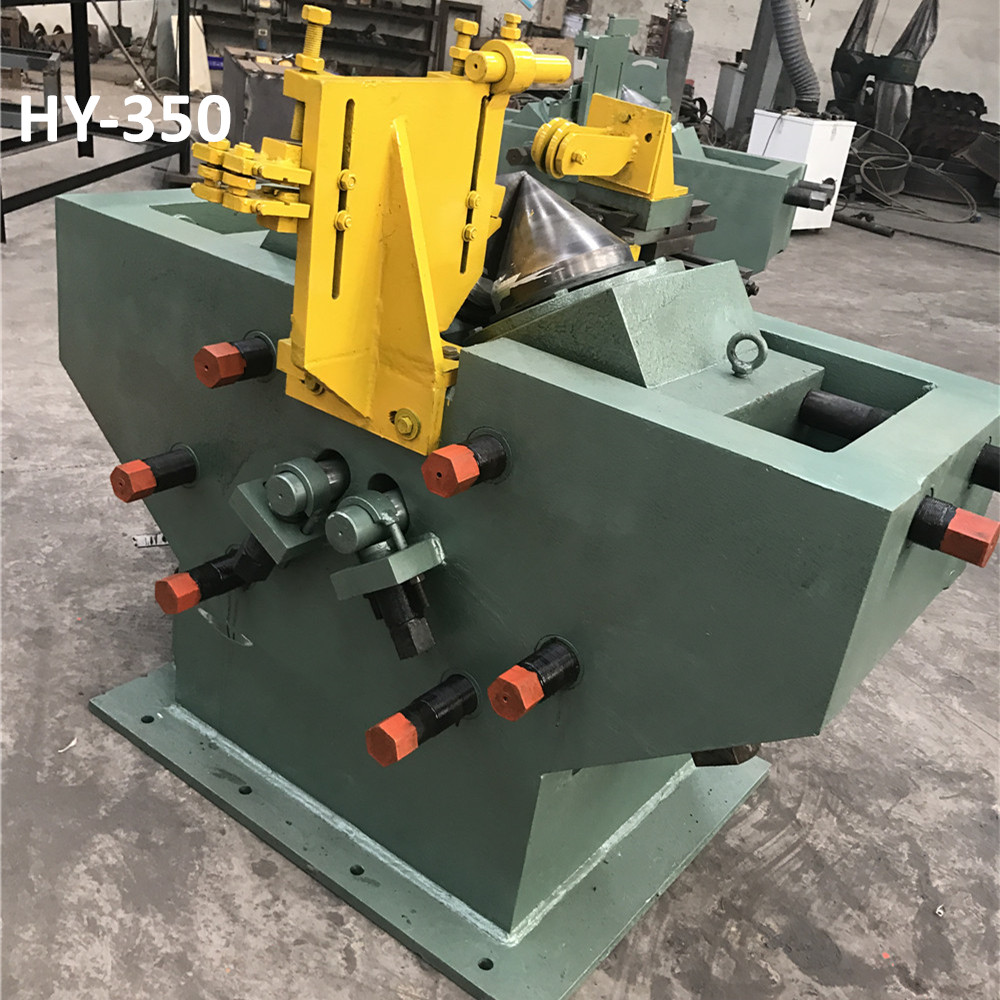
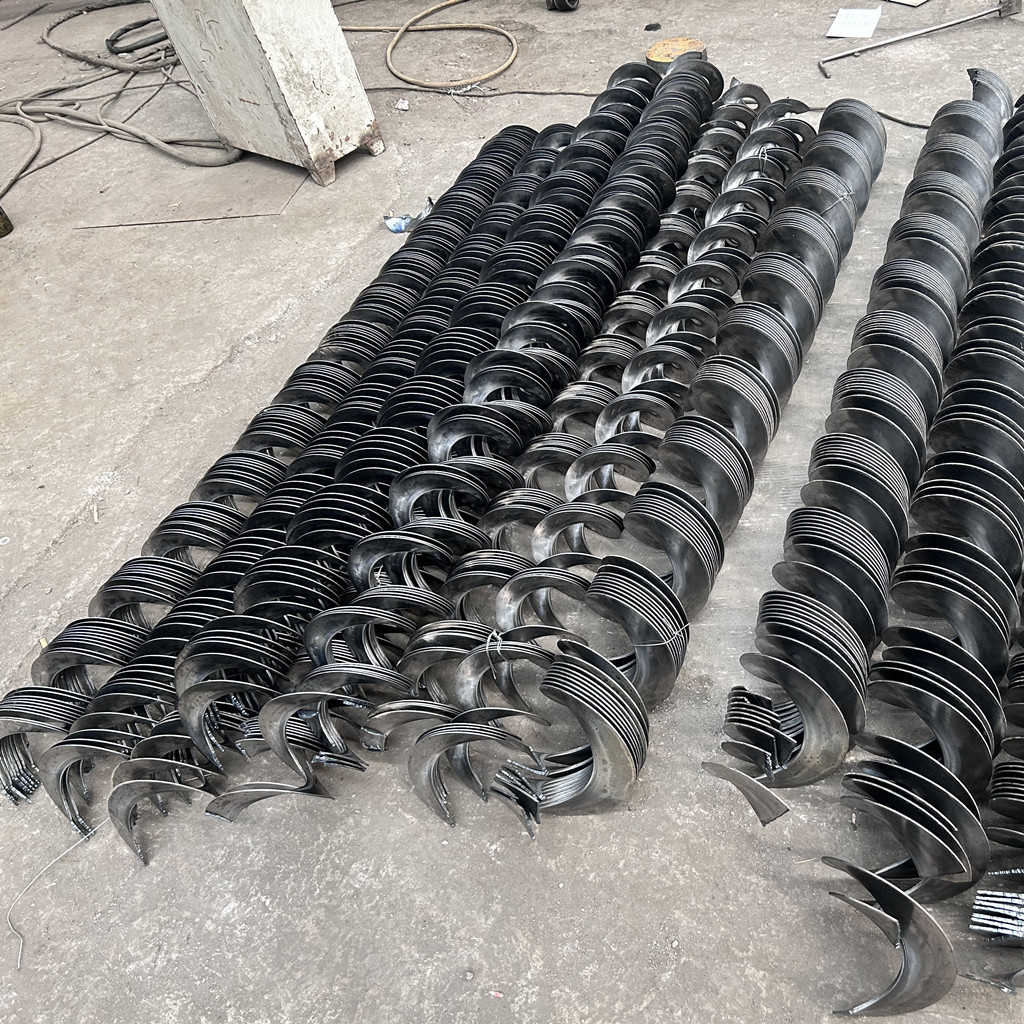
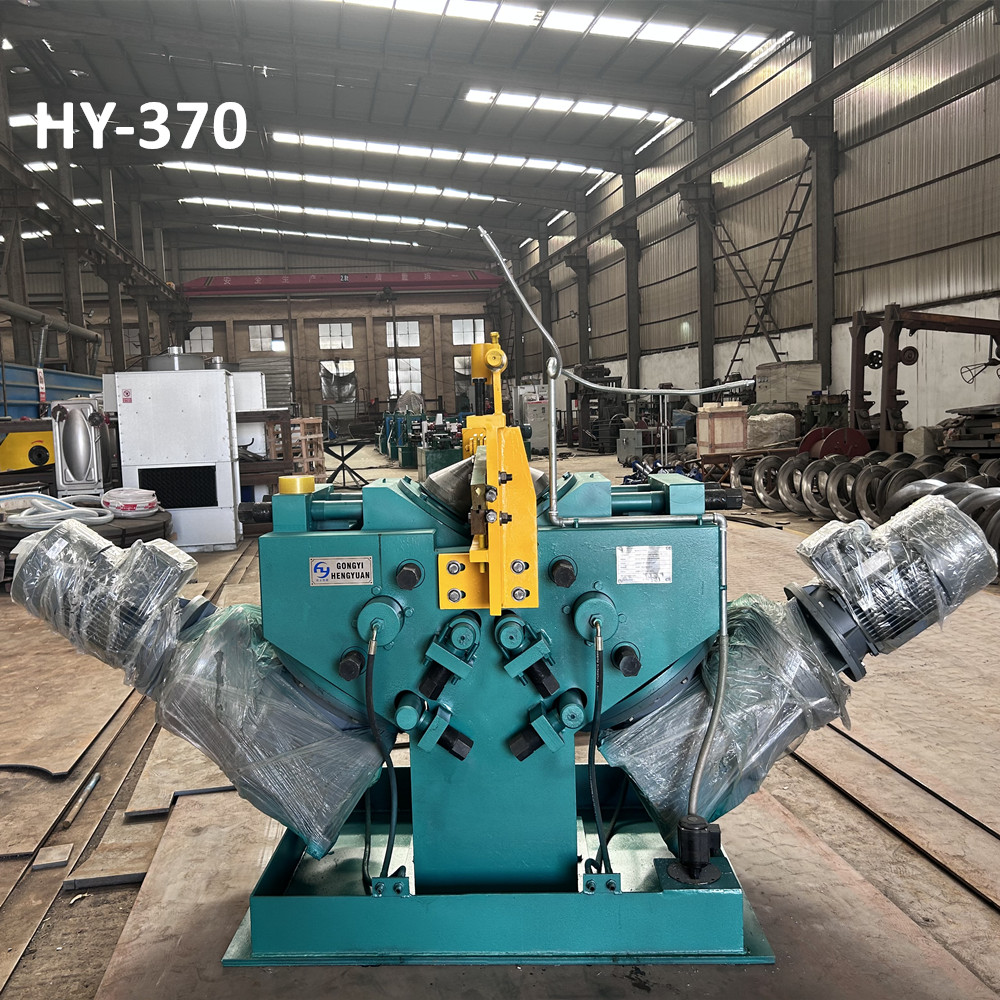
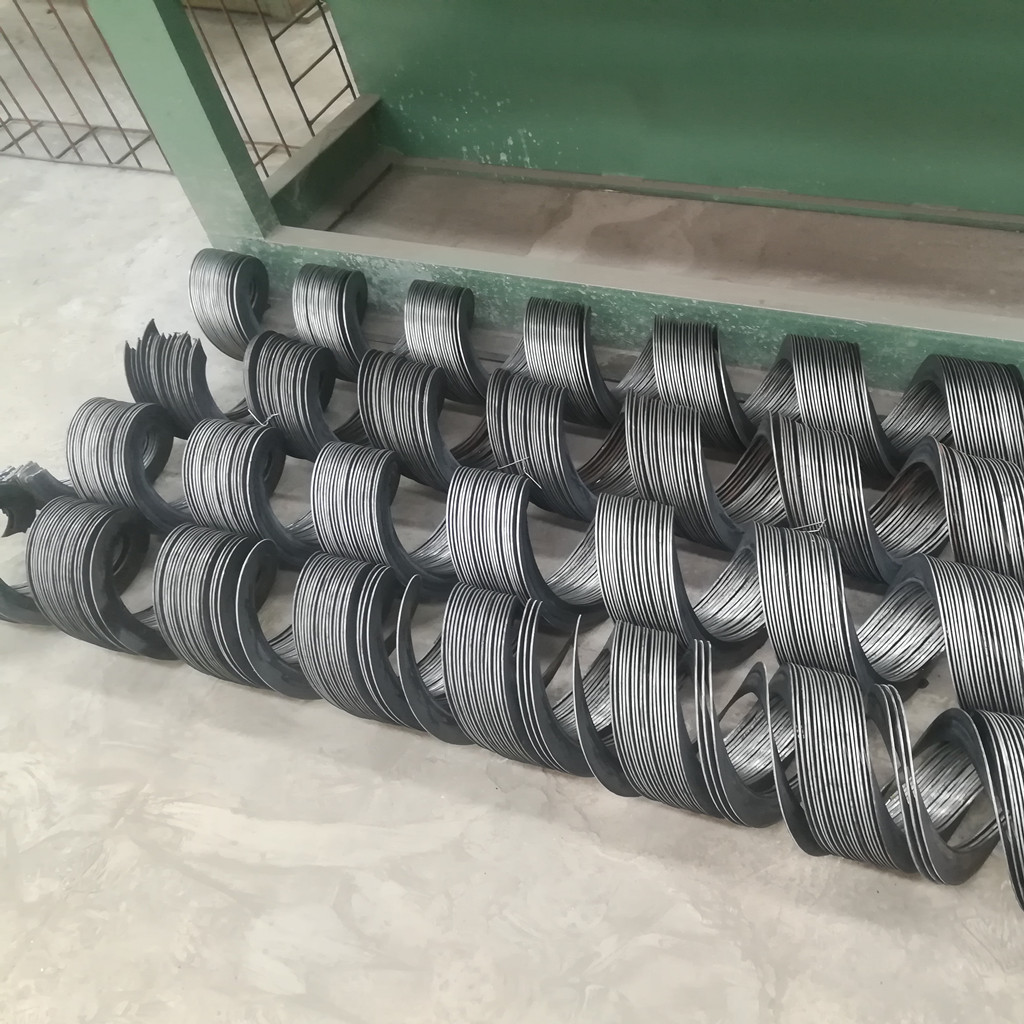
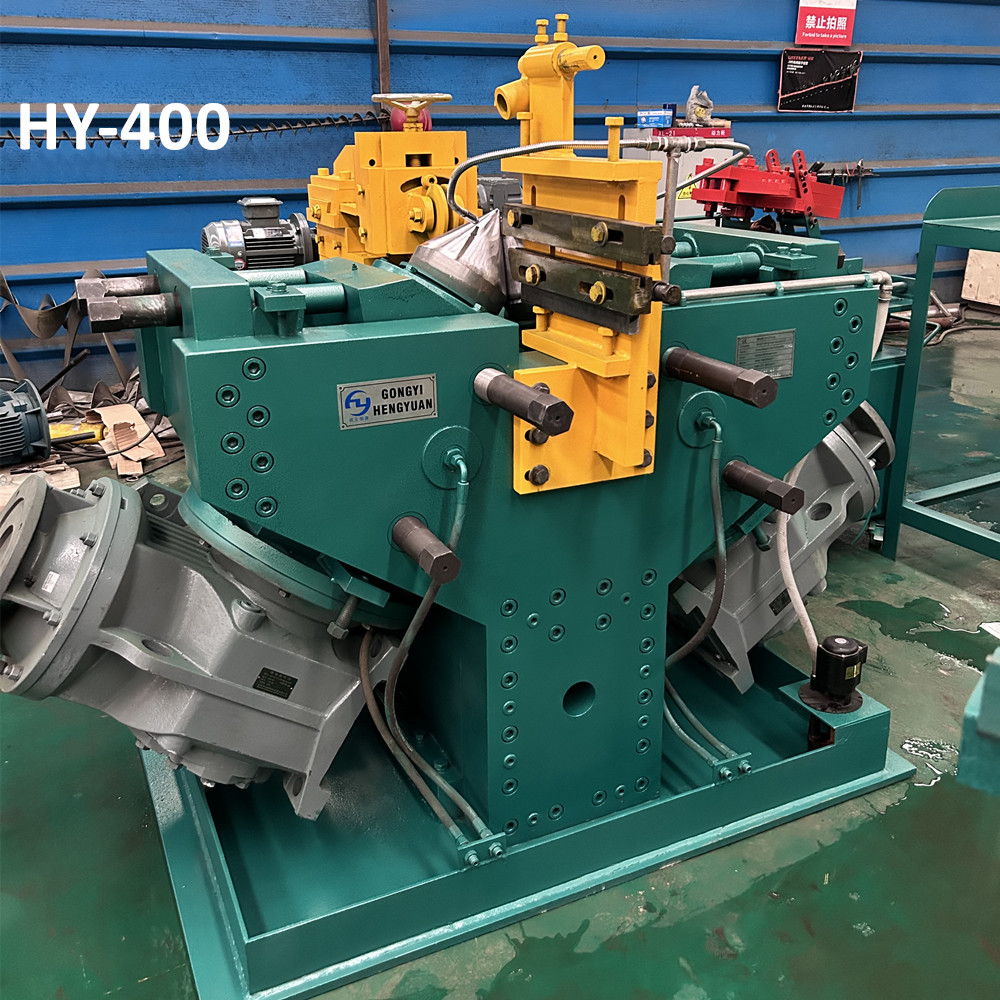
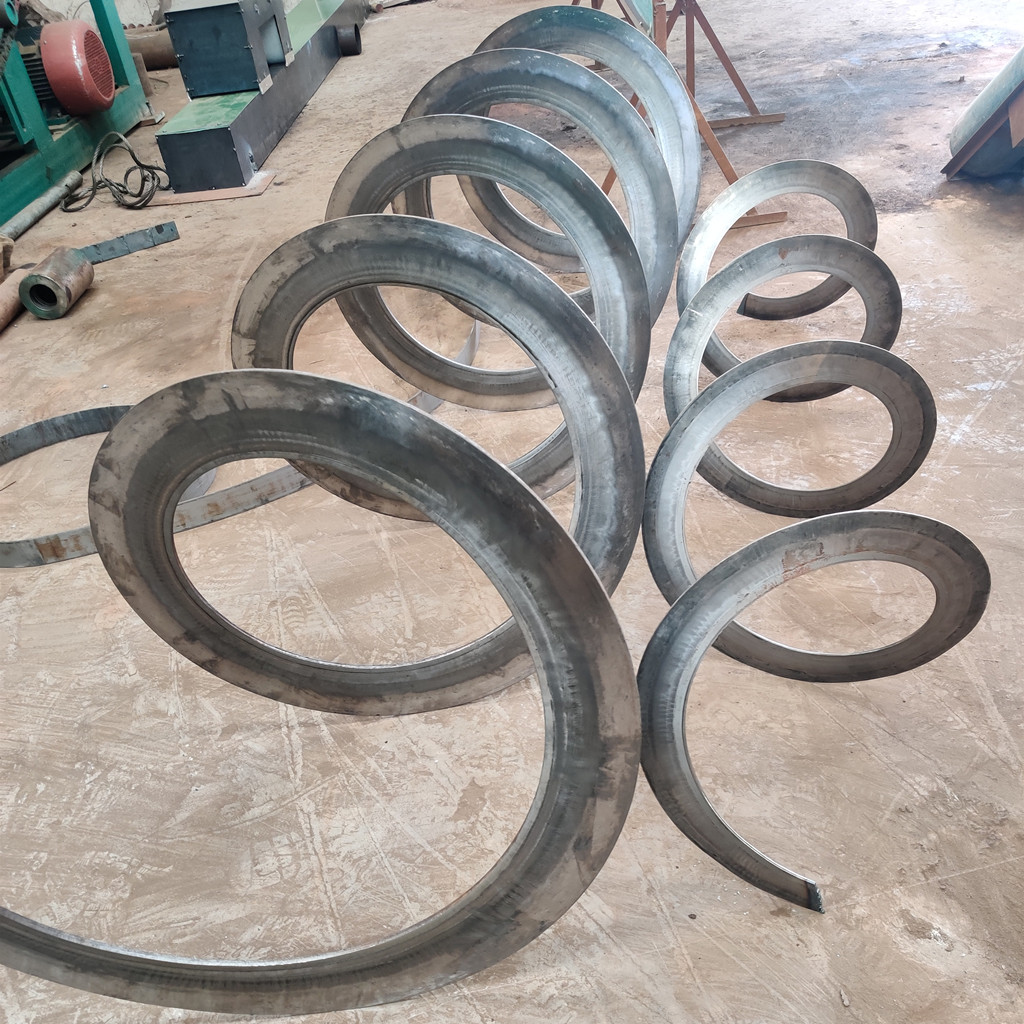
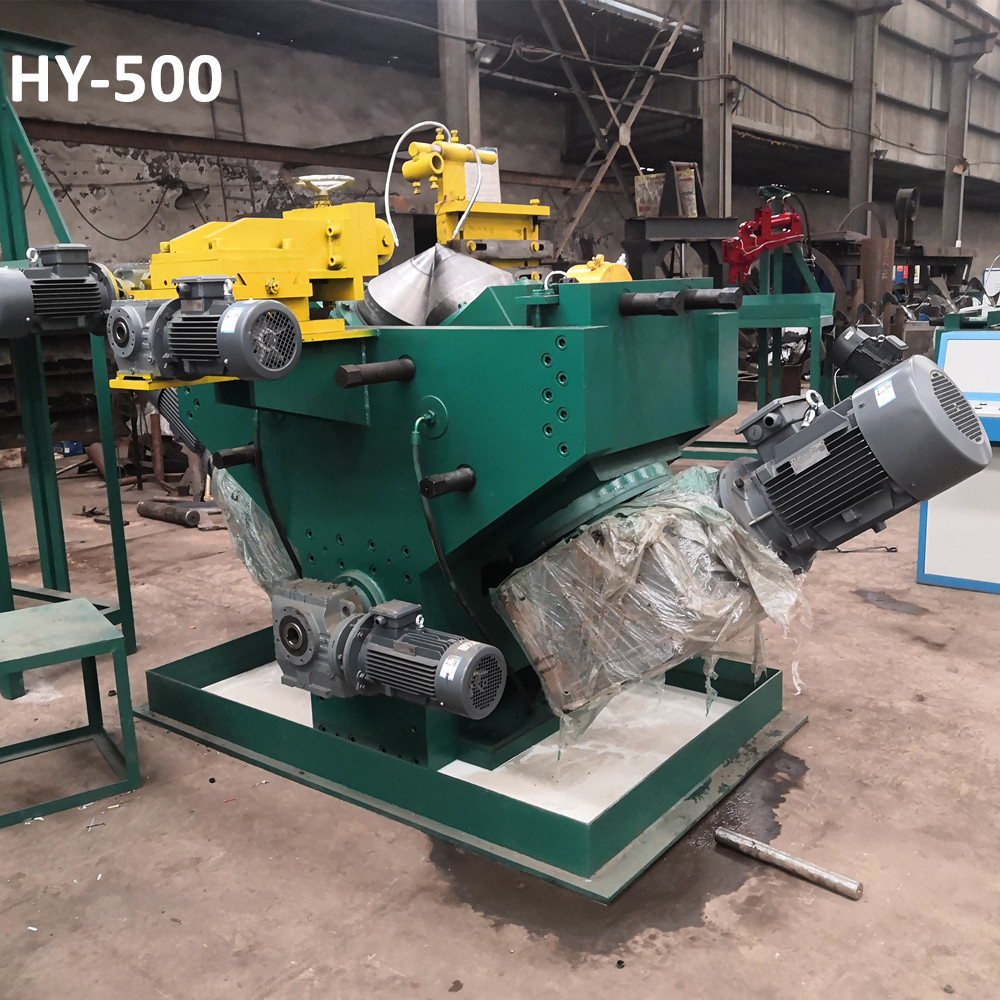
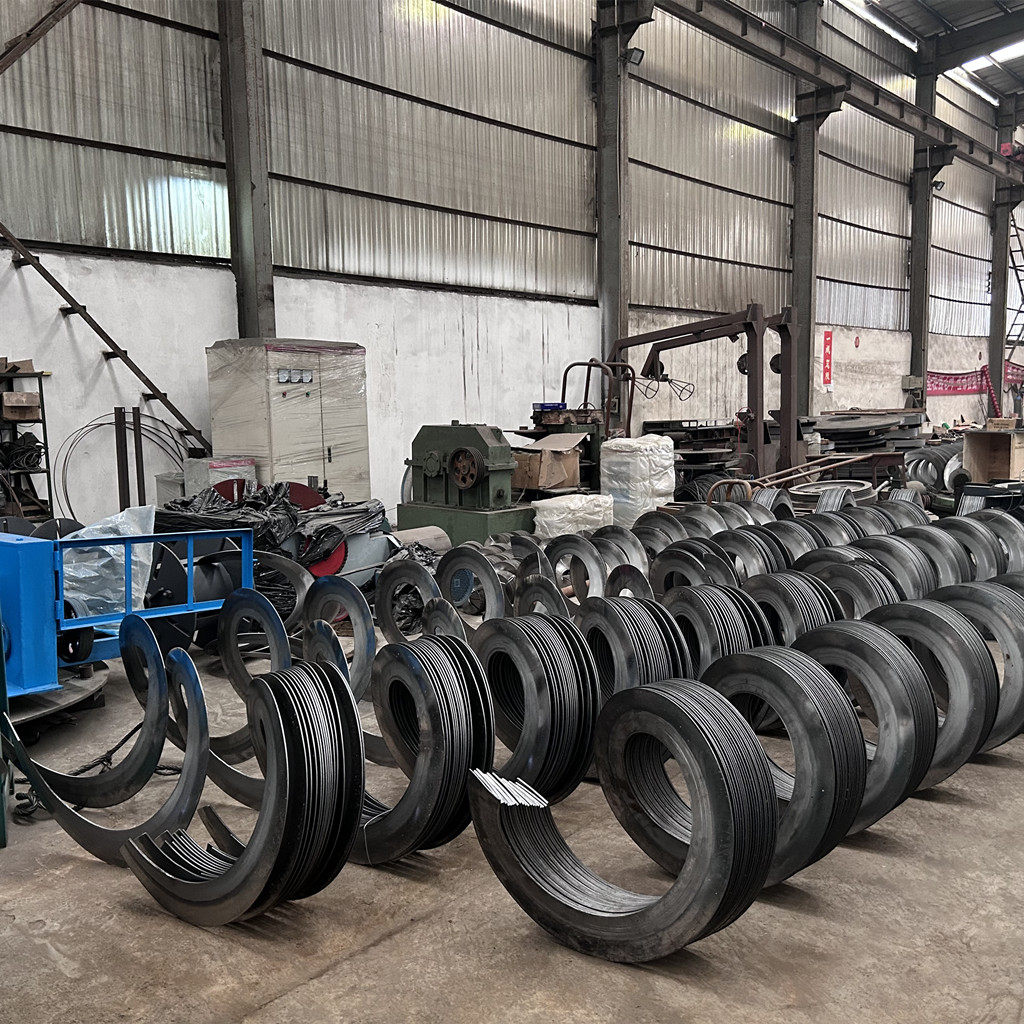
2.Sectional Auger Flight Machine
The sectional auger flight making machine is used for processing sectional augers. This line includes hydraulic system、mechanical system and electric control system. The hydraulic system drives moulds on the foundation to reciprocating move, and this makes two moulds interactional to change steel plate shape to be augers. This machine just needs one set mould to achieve multitudinous standard augers process. It is easy to operate, has high production efficiency and great working accuracy, and ect.
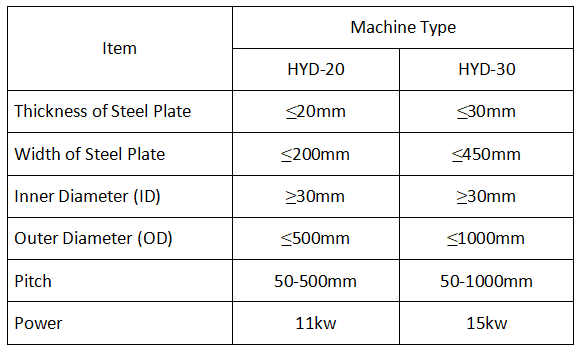
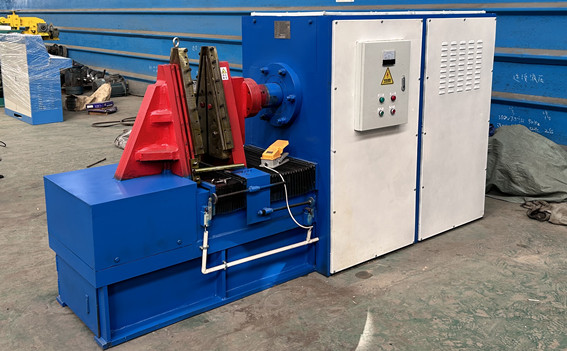
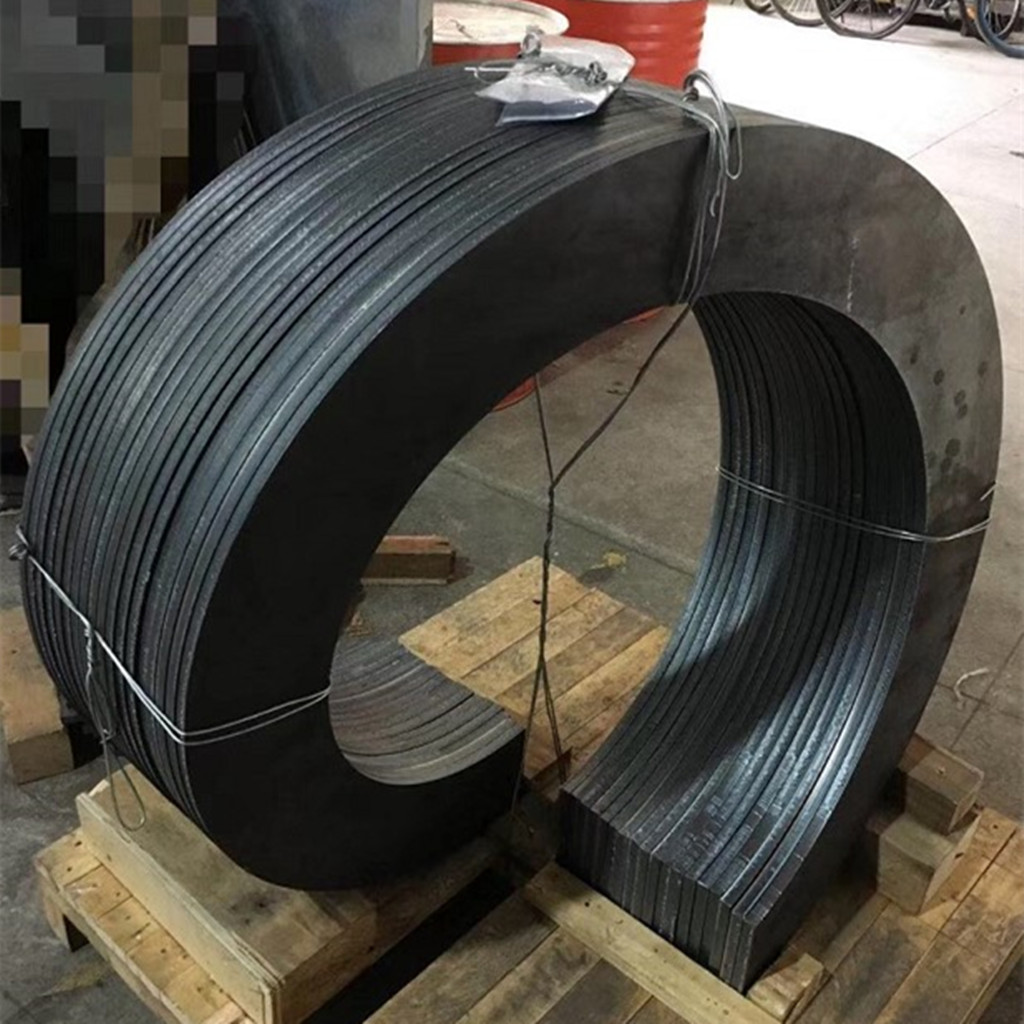
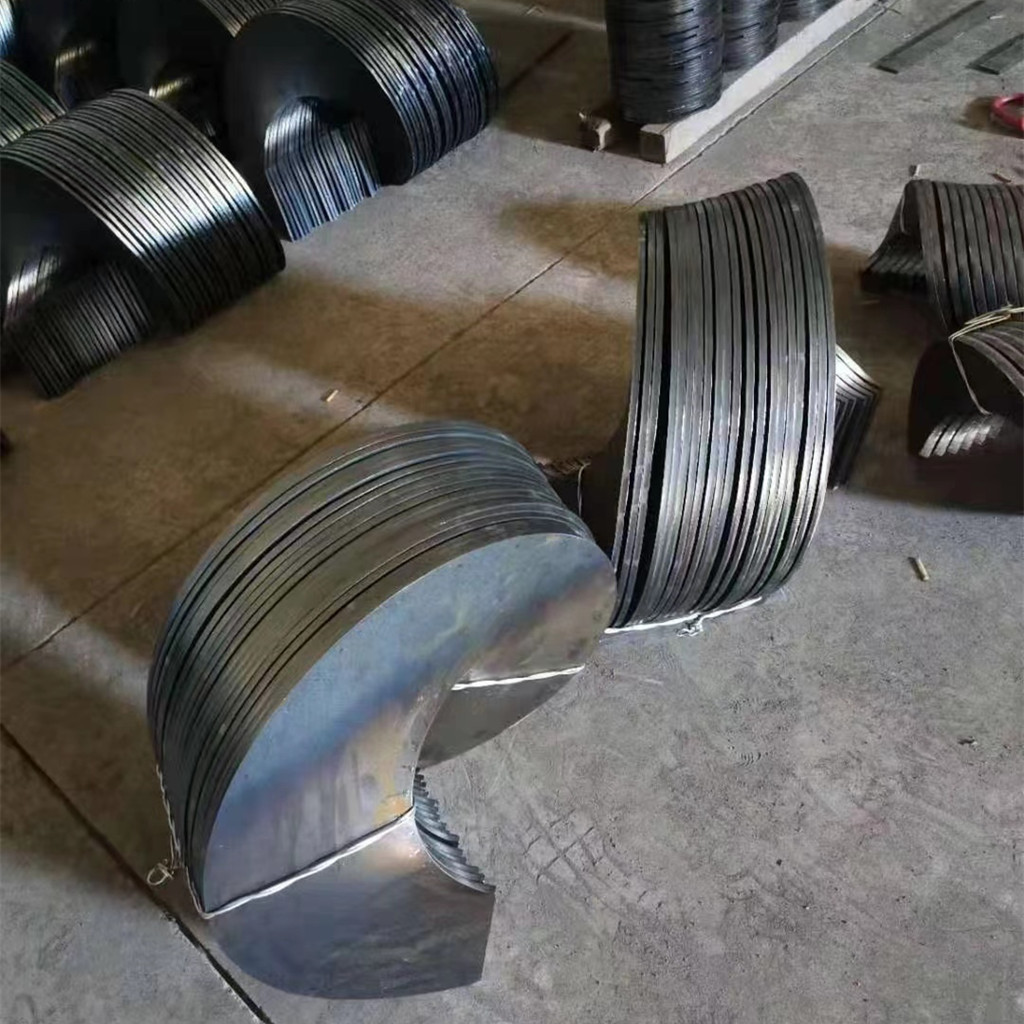
3.Spring Type Auger Flight Machine
The blades produced by the spring auger flight machine are widely used in various breeding machinery, livestock machinery, feed machinery, and screw conveying machinery. They are suitable for chicken, duck, pig, and grain suction machines. They can be used with pipelines to transport feed over long distances, feeding, thereby reducing labor and feeding intensity in the breeding industry, and realizing automated production in the breeding industry.
Spring auger flights are commonly known as screw conveyors. They are made of special spring steel and have no breakage, no deformation and long service life. According to the amount of feed, a variety of auger specifications can be selected in conjunction with the conveying pipeline. This product has simple structure, high performance, good durability and low failure rate, and is suitable for various feed breeding machinery. It installs a spiral spring in a plastic tube. The spring is directly driven by a motor and rotates at high speed in the plastic tube. Using the spiral spring conveying principle, when the hopper needs to be loaded, the motor is started to drive the spring to rotate, and the raw materials are moved by the spring spiral. The inlet end of the plastic pipe is aligned with the hopper. There is a discharge port, and the raw materials moved to the discharge port are moved by the spring. The centrifugal force of rotation throws the material out of the discharge port and into the hopper. This kind of feeding device has a simple structure, is easy to operate and maintain, and is suitable for conveying granular materials and powder. The direction of rotation of the screw conveyor’s rotating shaft determines the conveying direction of the material, but generally the screw conveyor is designed to rotate the steel wire according to single transport.
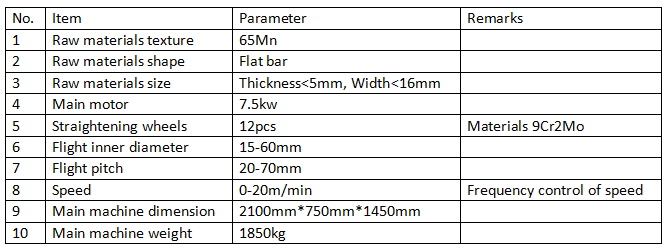
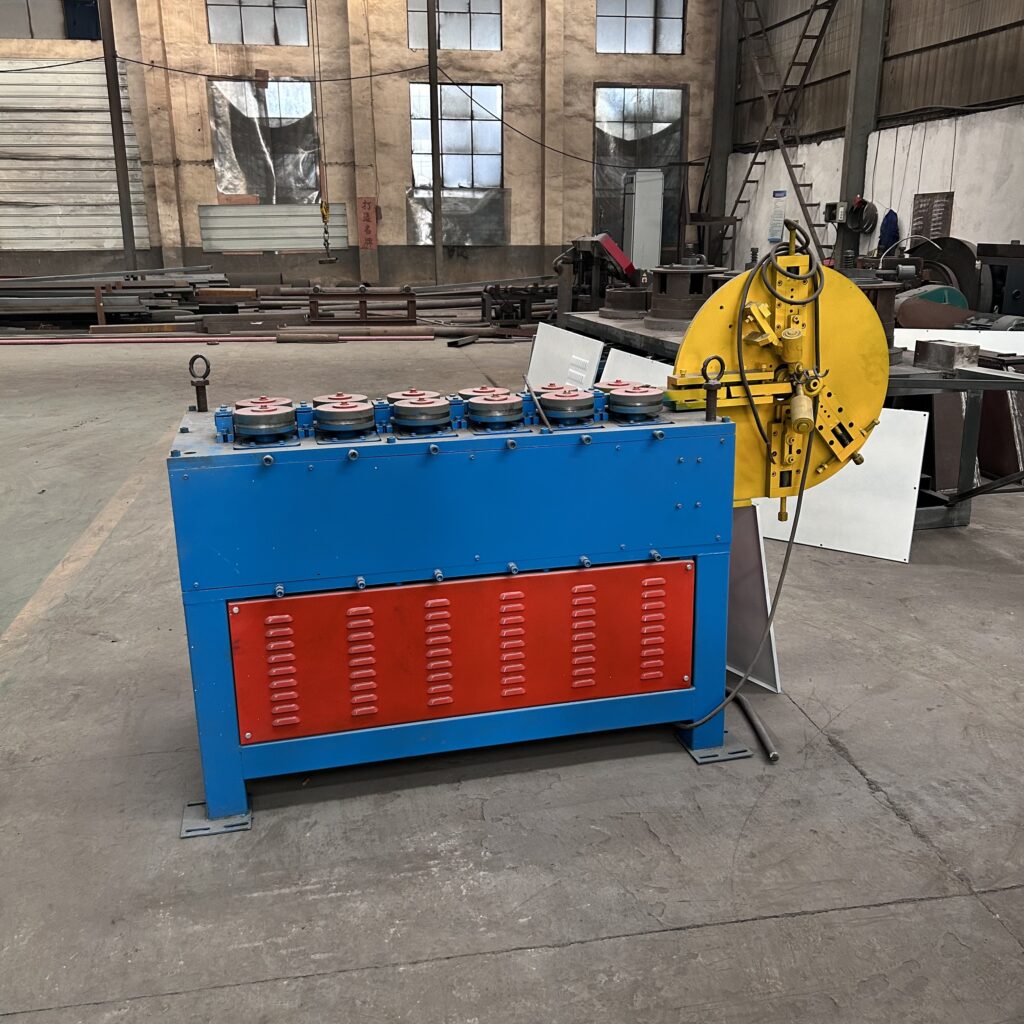
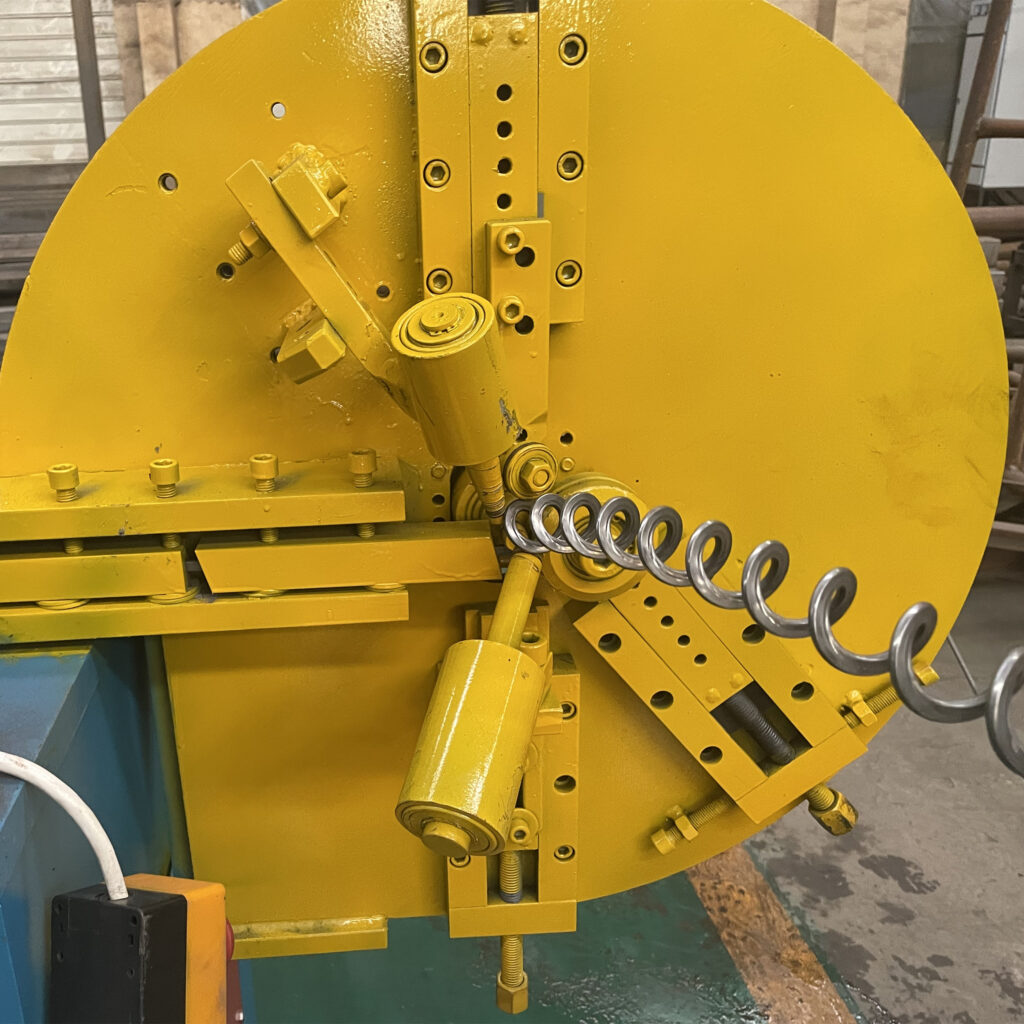
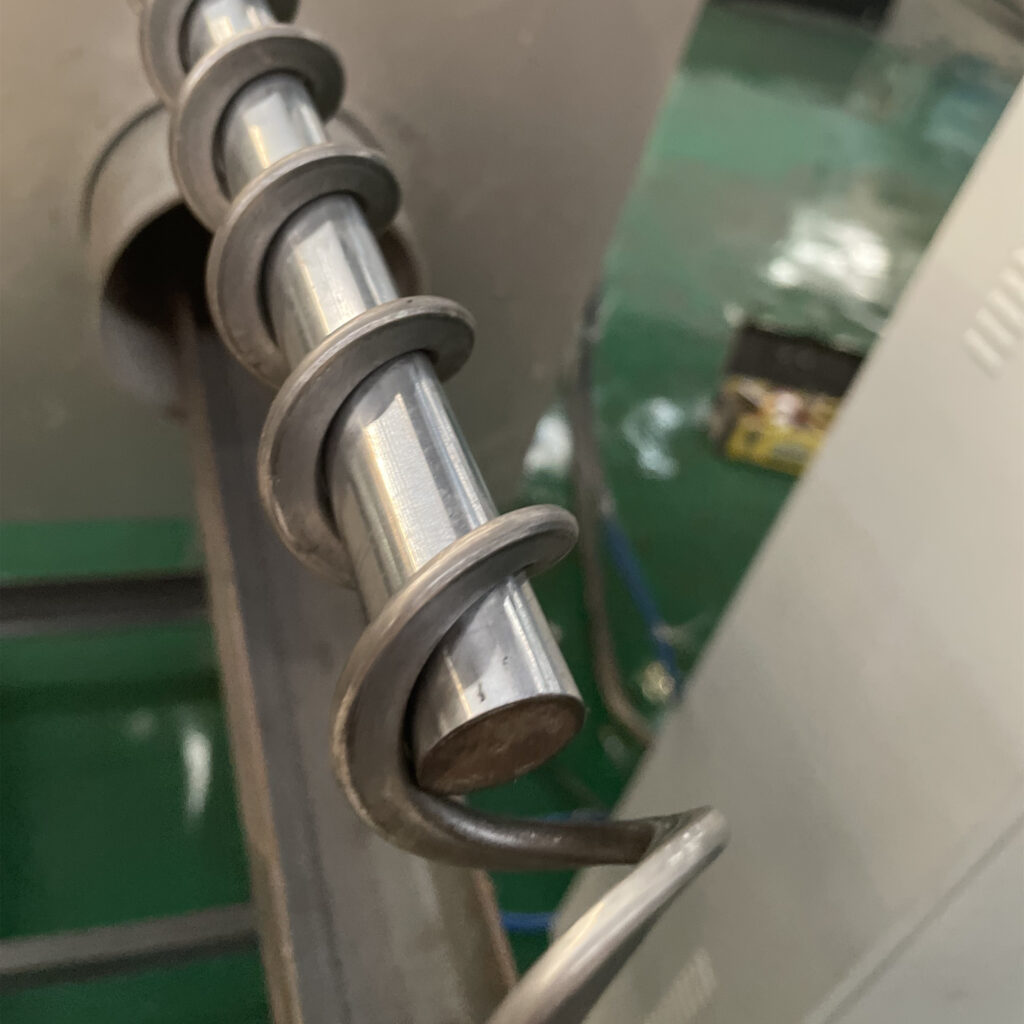
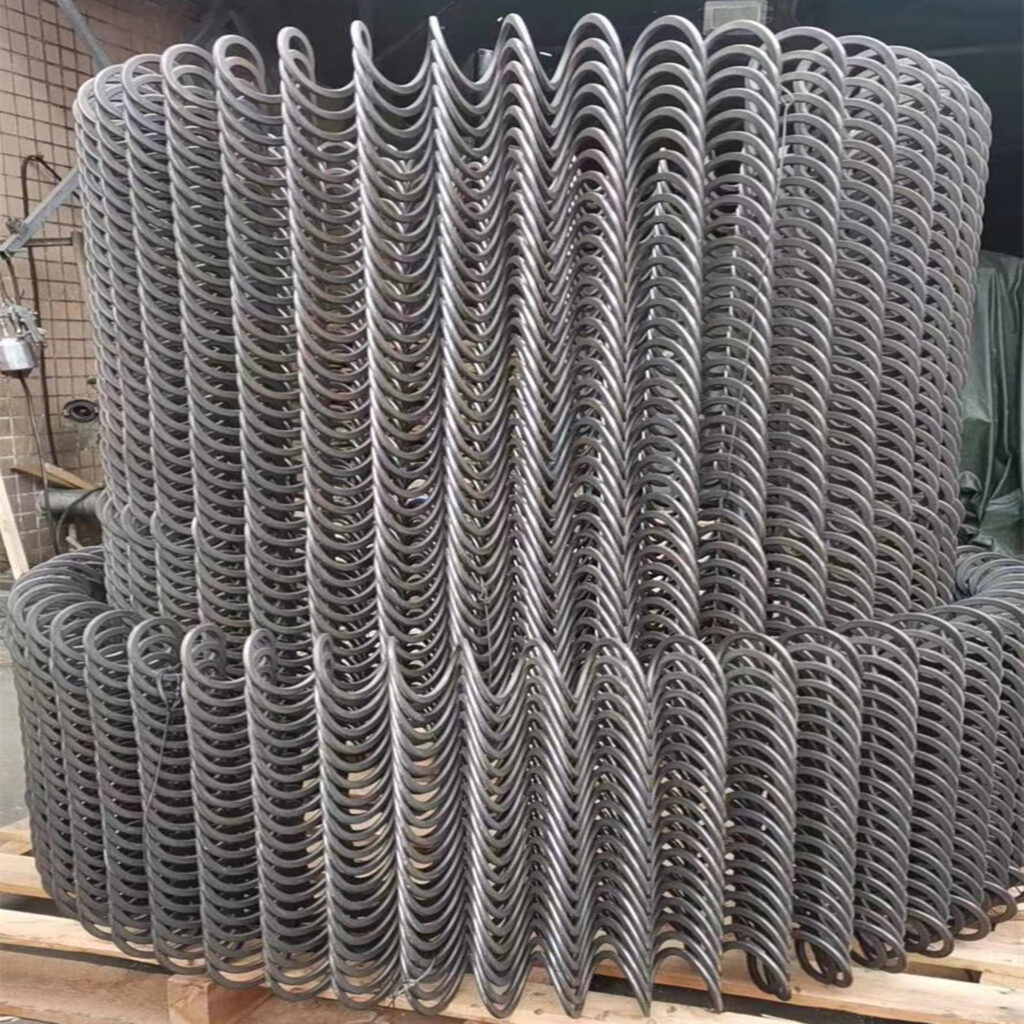
4.Lathe Type Auger Flight Machine
This machine produces same thickness screw flights, and it mainly includes control system and mechanical system. The control part is servo system to produce different size screws; Put data(ID, OD, and pitch) on the screen, the mechanical parts will be adjusted automatically, the could produce corresponding size screw. The mechanical part includes slipping track, lead screw, supporting frame and dabber. To produce different size screw, it needs to change different dabber. Different pitch with match different speed.
The machine operates on the principle of a lathe, where a piece of metal is shaped and cut to form the spiral flights with exacting precision. This process involves the deformation of a flat steel plate into a helix of desired diameter and pitch, ensuring a snug fit and seamless integration into the screw conveyor’s shaft. Unlike traditional methods, which can be labor-intensive and prone to inaccuracies, the lathe-type auger flight machine automates the process, significantly enhancing production speed, consistency, and quality of the flights.
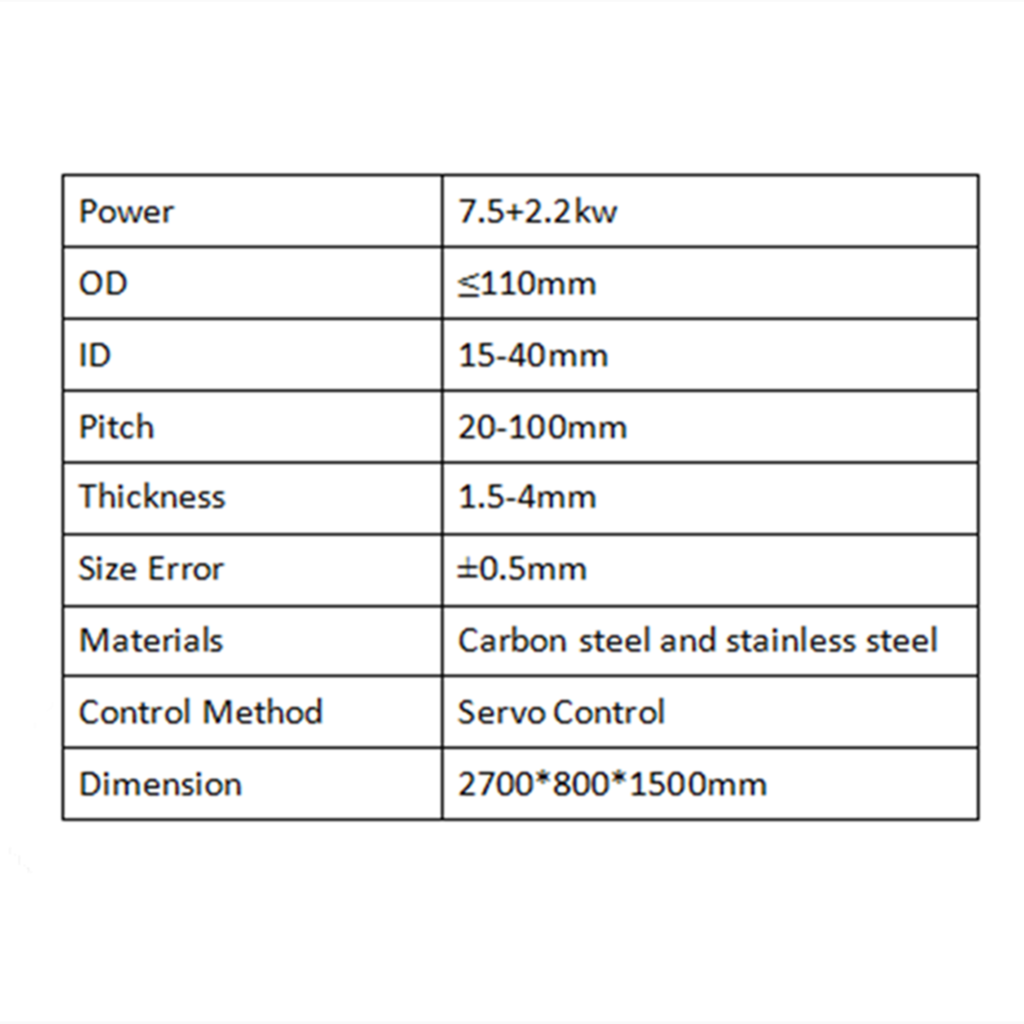
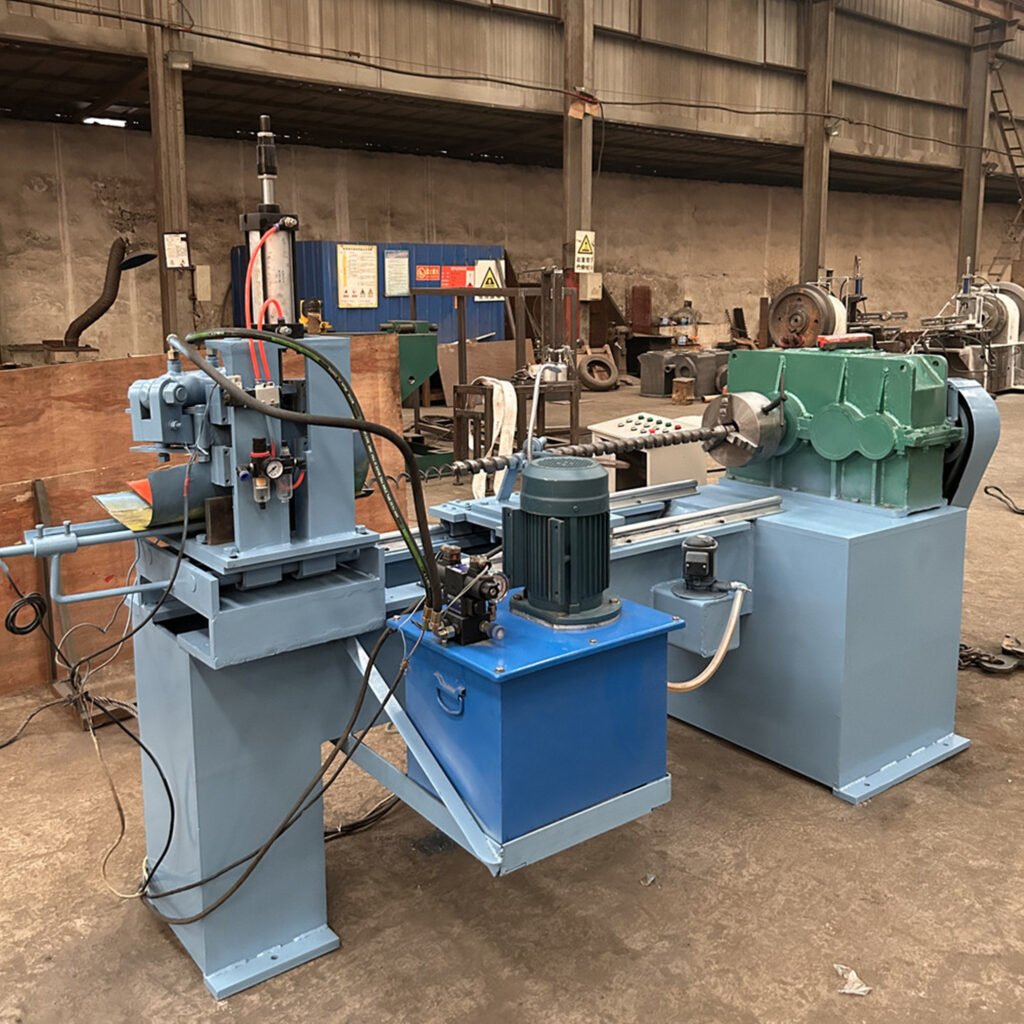
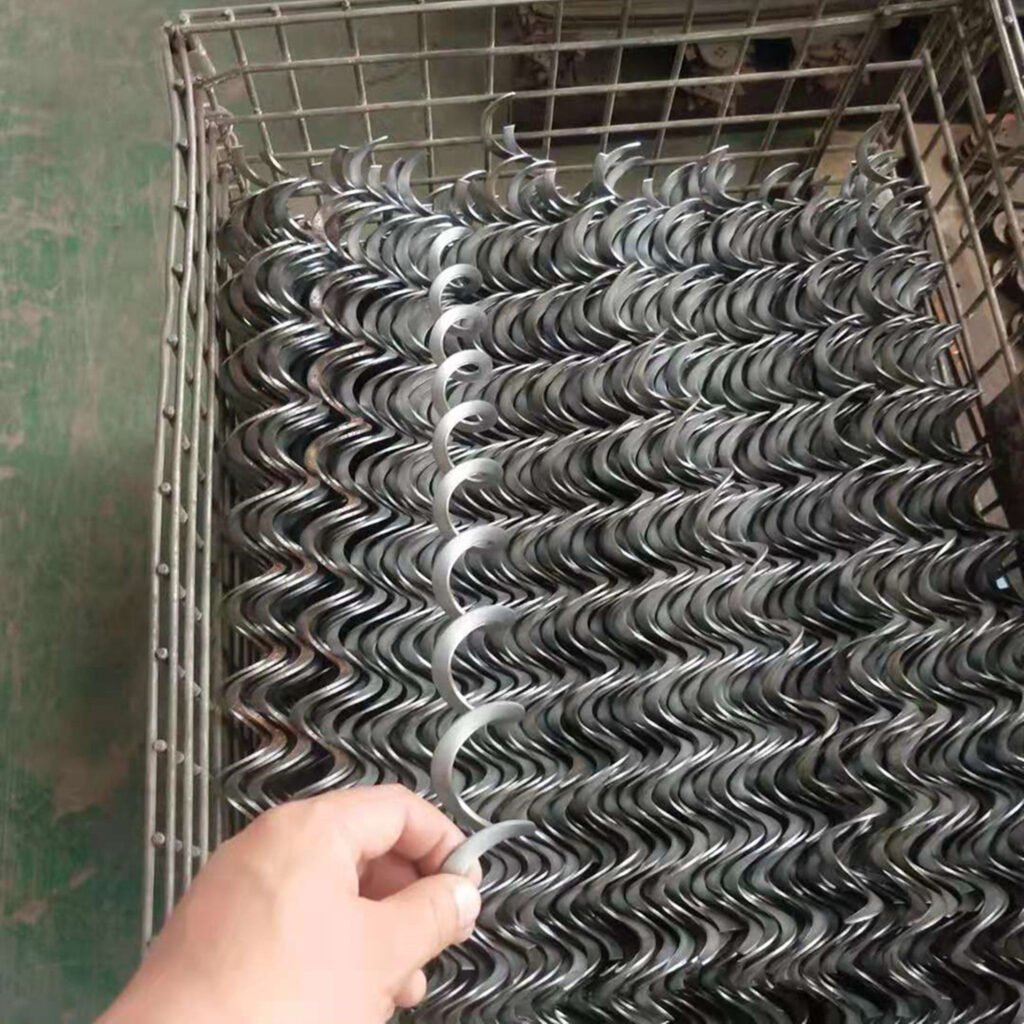
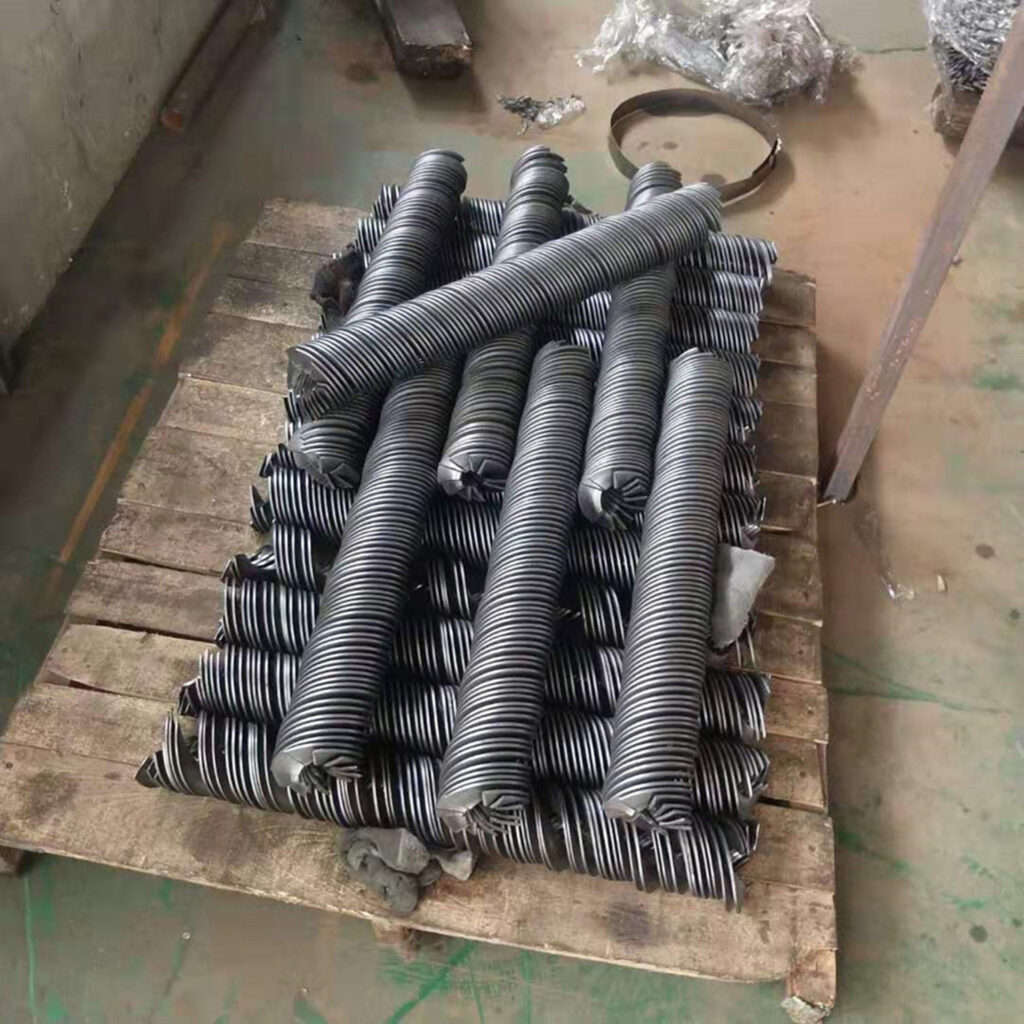
5.Pipe Contracted and Shrinking Machine
In the realm of industrial manufacturing, precision and efficiency are paramount, especially when crafting components essential for cutting-edge technologies like solar panels. Among the array of specialized machinery designed to meet such demands, the pipe contracted and shrinking machine stands out as a vital tool. This innovative equipment plays a pivotal role in shaping raw materials into cone-shaped pipes, specifically tailored for integration within solar panel frameworks. By harnessing advanced engineering principles, this machine not only ensures dimensional accuracy but also facilitates the seamless assembly of solar panels, contributing to the advancement of renewable energy solutions. In this introduction, we delve into the functionalities, significance, and applications of the pipe contracted and shrinking machine within the context of solar panel production.
Semi-Automatic Type
This type of machine integrates manual operations into its workflow, requiring operators to manually heat and feed pipes into the system. Despite its reliance on manual intervention, the semi-automatic pipe contracted and shrinking machine offers a unique blend of precision, flexibility, and efficiency, making it an ideal choice for various manufacturing environments. This introduction explores the intricacies of semi-automatic machinery, shedding light on its functionalities, benefits, and applications, particularly in the context of shaping pipes for specialized purposes such as solar panel construction.
Fully-Automatic Type
In the realm of modern industrial manufacturing, the demand for streamlined processes and increased efficiency drives the evolution of machinery. Among these innovations, the fully automatic pipe contracted and shrinking machine stands as a pinnacle of technological advancement. This sophisticated piece of equipment epitomizes precision and automation, seamlessly orchestrating every step of the pipe contracting and shrinking process with minimal human intervention. From heating to feeding and shaping, this machine operates autonomously, harnessing cutting-edge technology to deliver consistent and high-quality results.
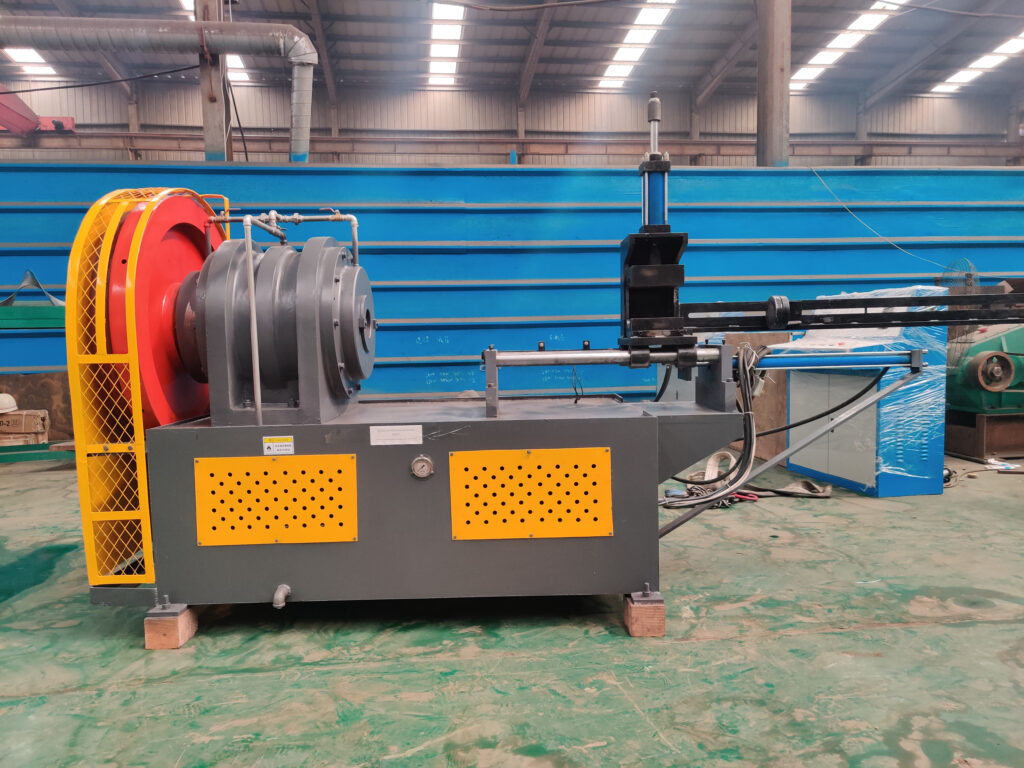
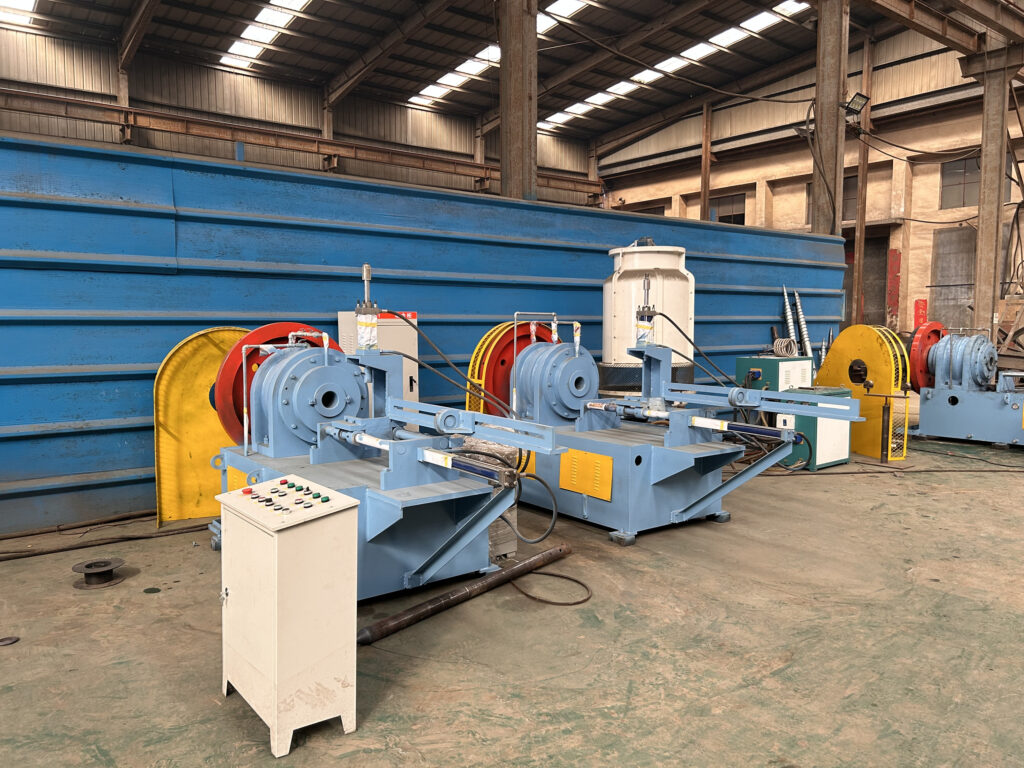
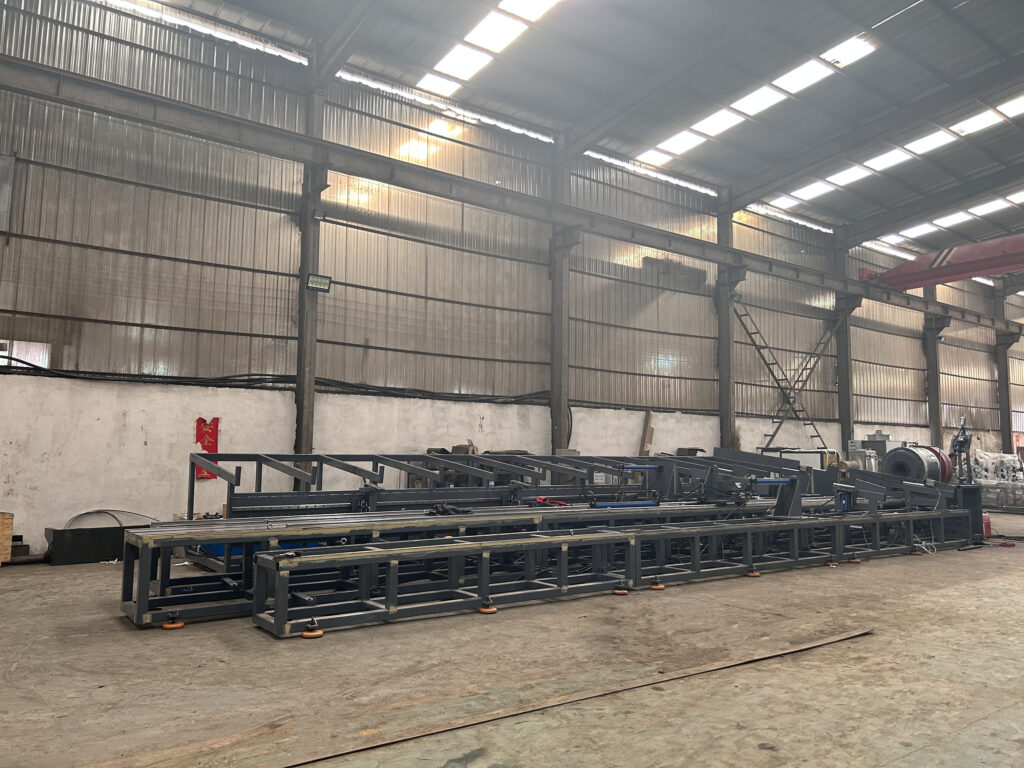
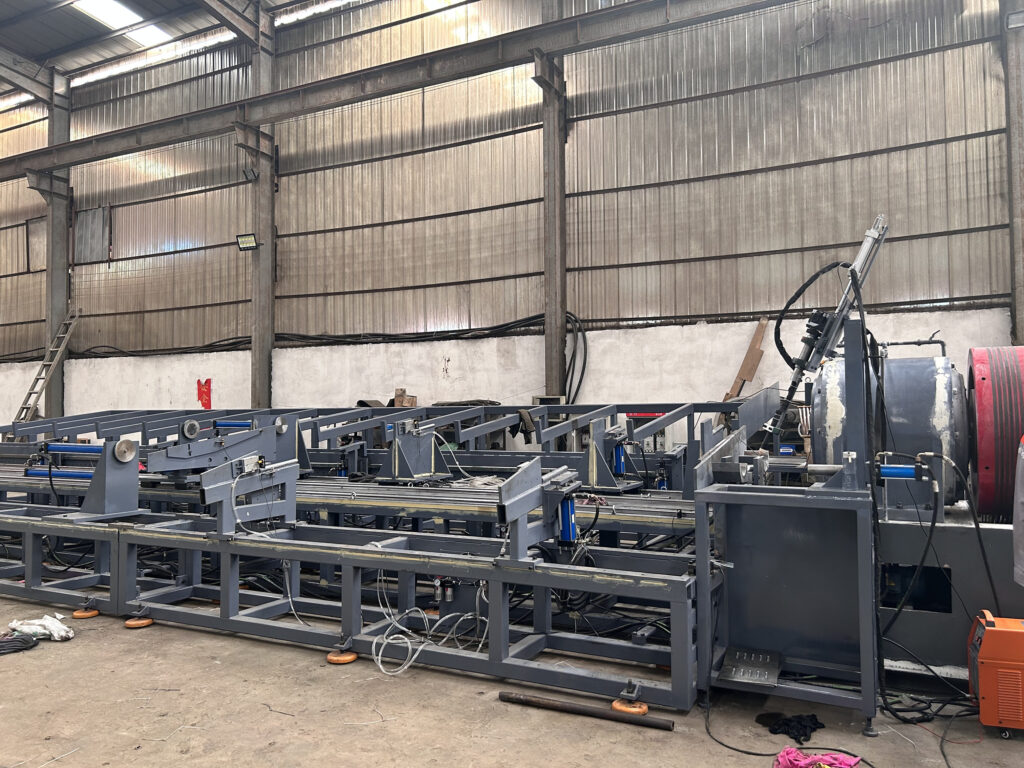
Advantages
1.Solar Panels helical Piles machine is suitable to process conical metal tubes;
2. We can do it as manual and automatic way when it works, It has the characteristics of low noise, easy operation, high yield and stable;
3. Forming one pieces pipe, the time is short, high efficiency, pipe surface is smooth with out scars;
4. The machine mold is easy to change, and different shapes of metal tubes can be processed with the corresponding mold to meet different needs.
5. Suitable for special customized taper molding.
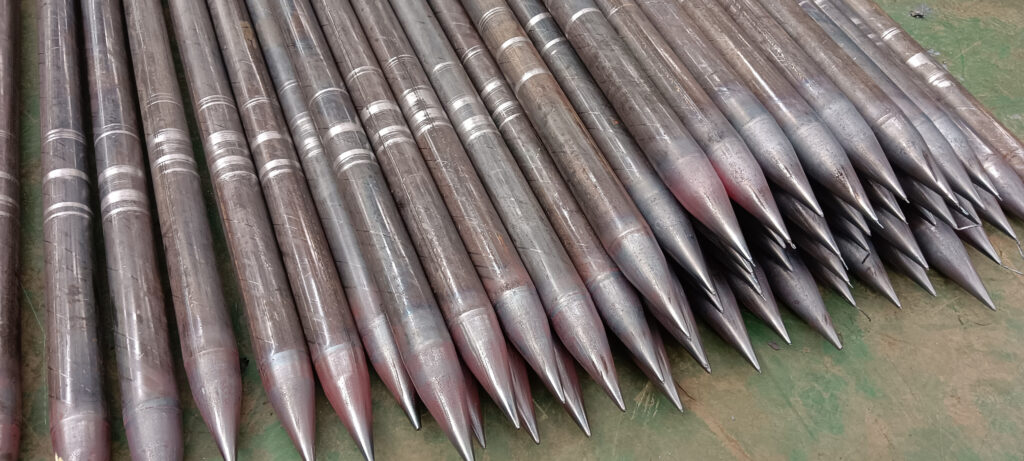
Cone after Welding Auger Flight and Galvanization
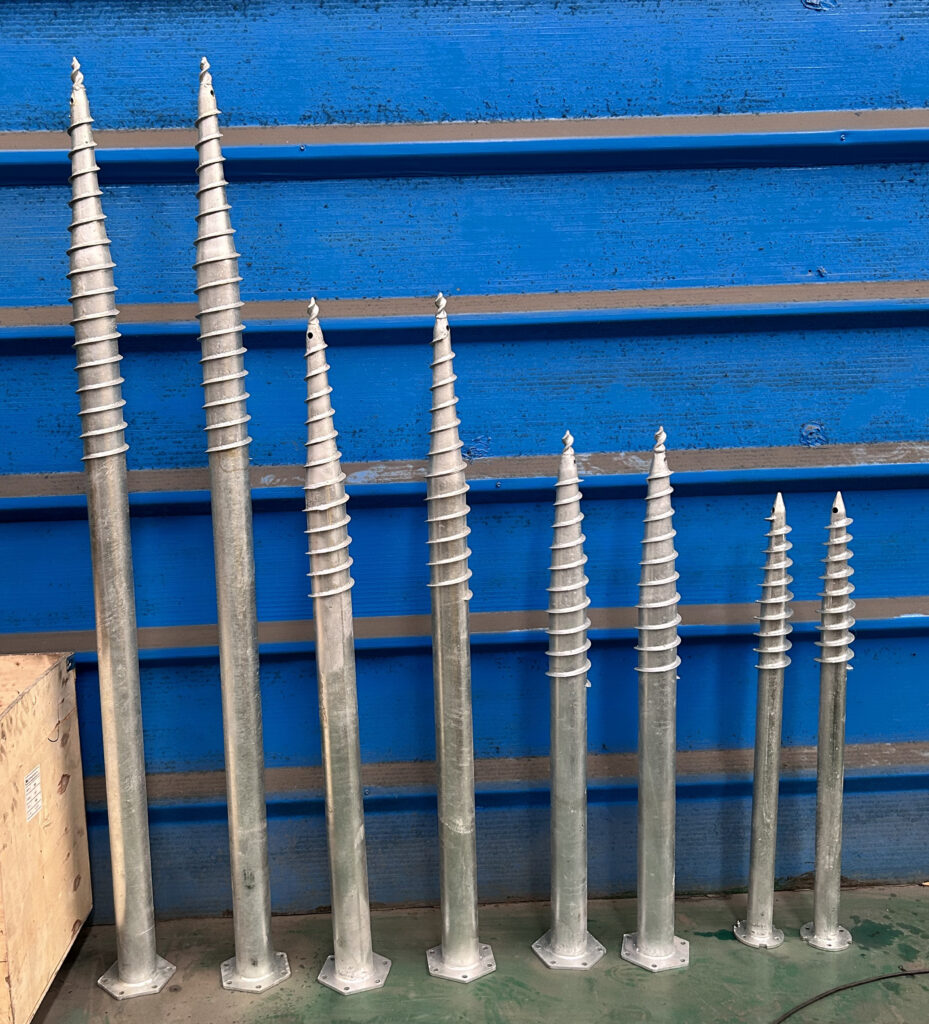
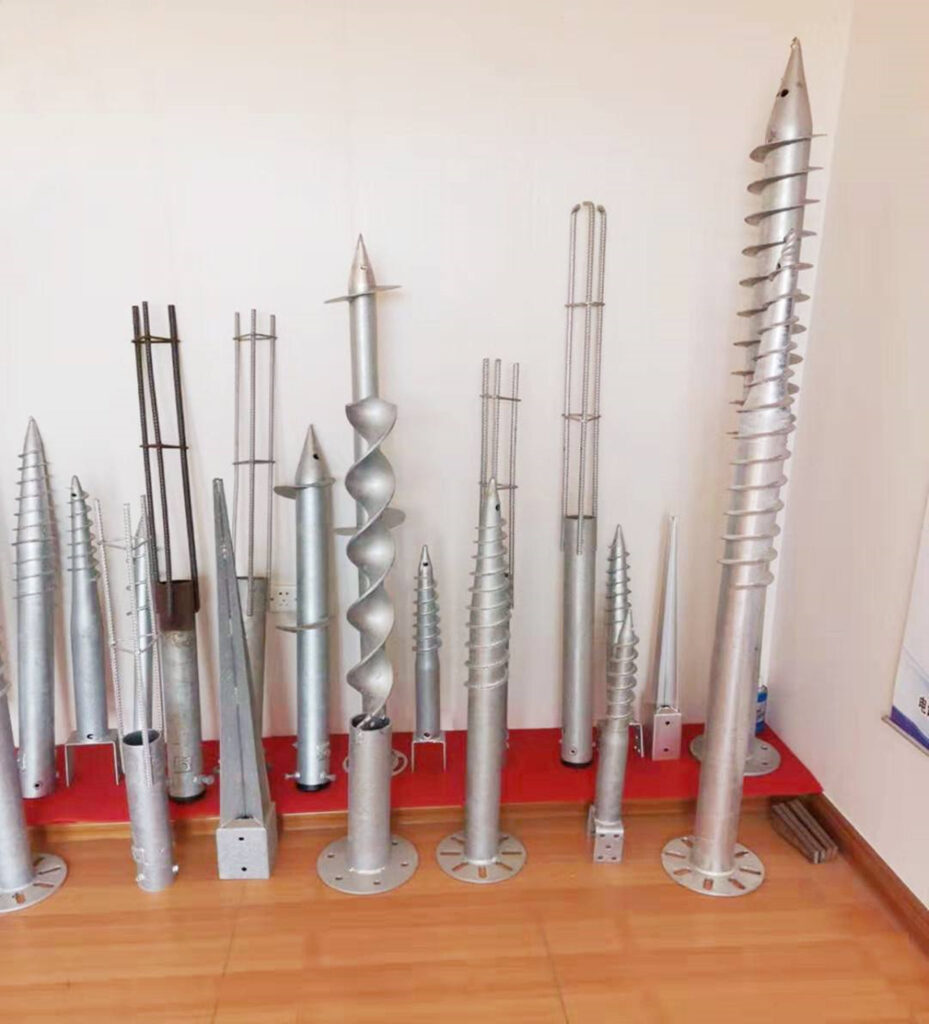
6.Auger Flight Welding Machine
In the domain of industrial fabrication, precision and durability are essential, particularly in the assembly of machinery crucial for material handling and processing. Among these, the auger flight welding machine emerges as a fundamental tool, designed to weld auger flights onto pipes with precision and efficiency. Auger flights play a critical role in conveying and mixing materials in various industries, including agriculture, construction, and mining. The auger flight welding machine streamlines this process by seamlessly affixing flights onto pipes, ensuring structural integrity and longevity.
This introduction delves into the functionalities and significance of the auger flight welding machine, highlighting its role in enhancing the performance and reliability of auger-based systems. From its automated welding capabilities to its adaptability across diverse applications, this machine represents a cornerstone in modern industrial fabrication, facilitating the seamless integration of auger flights onto pipes to meet the demands of various sectors.
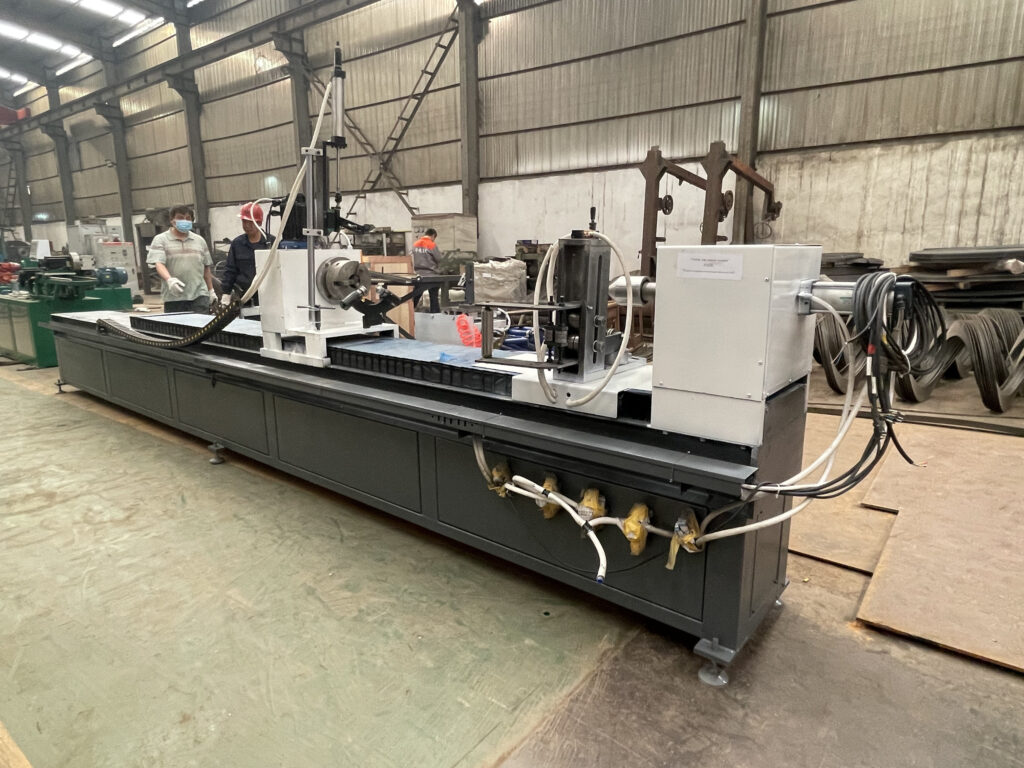
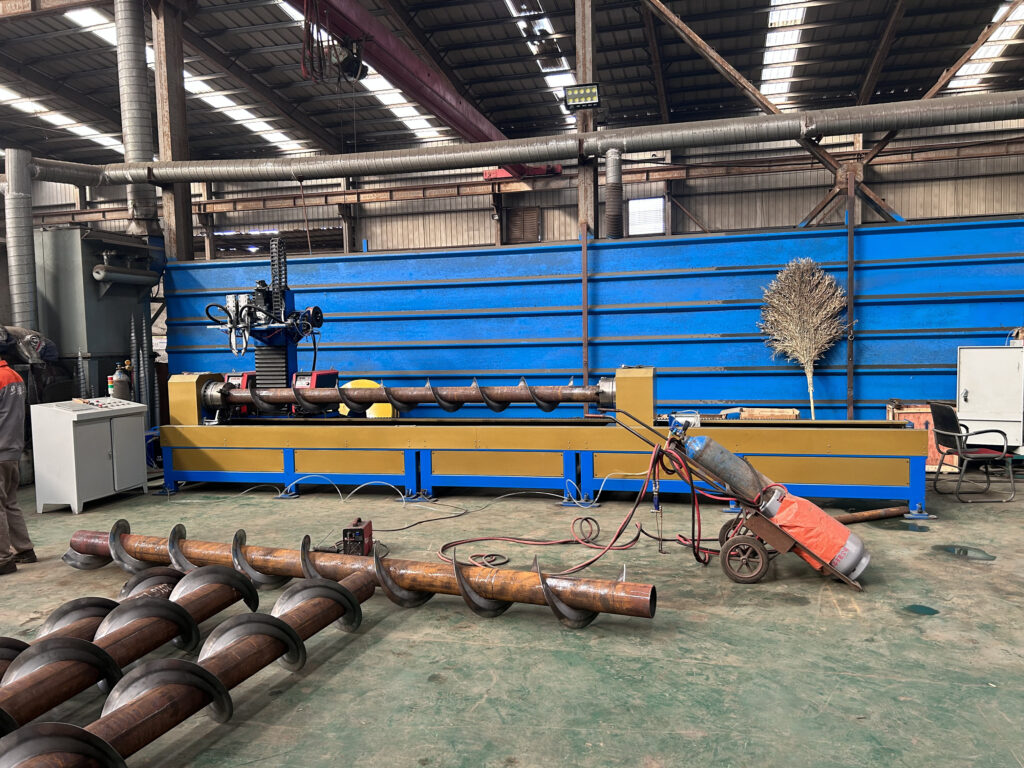
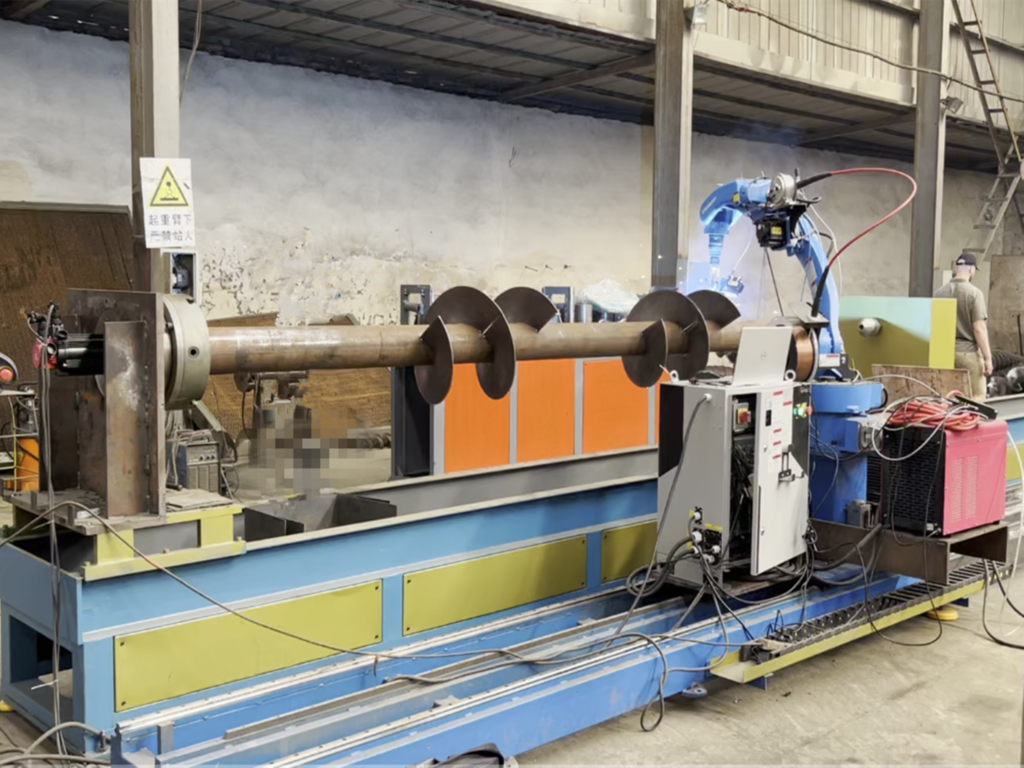
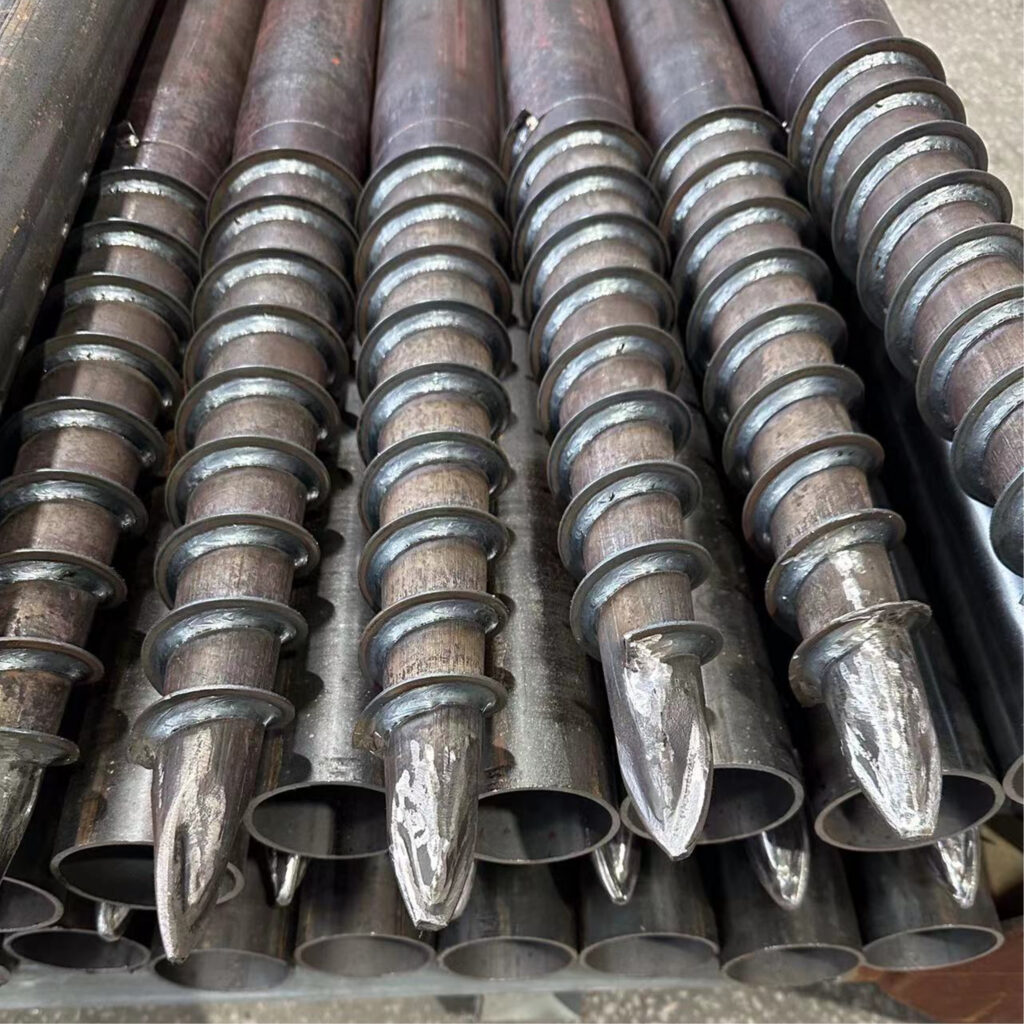
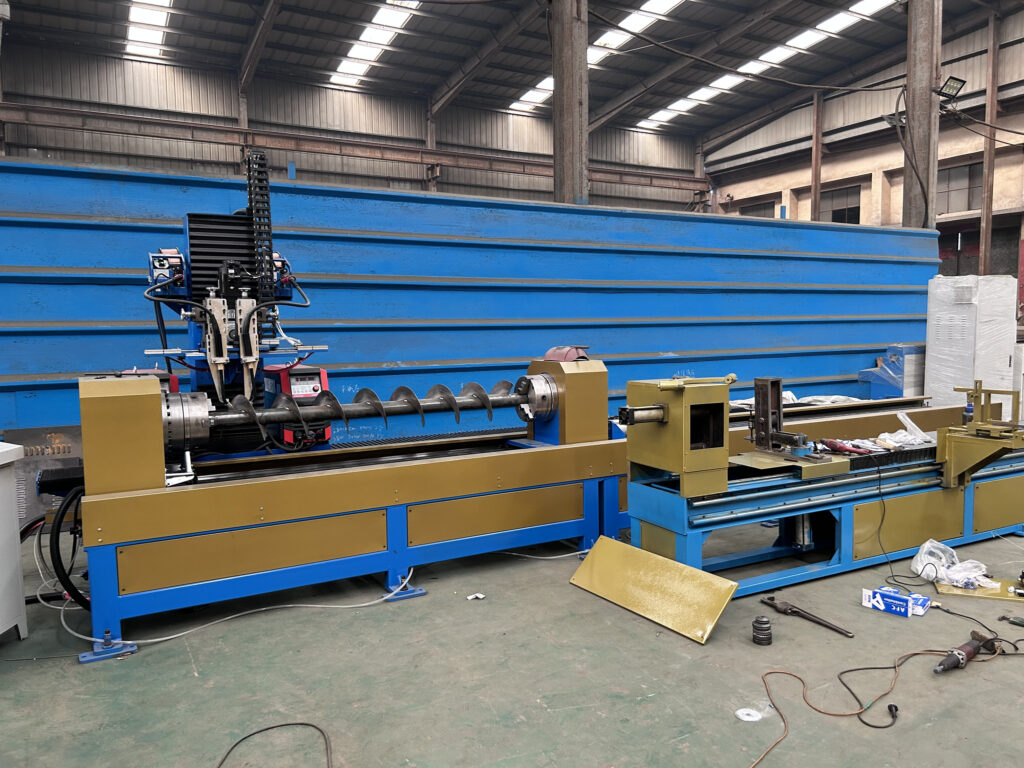
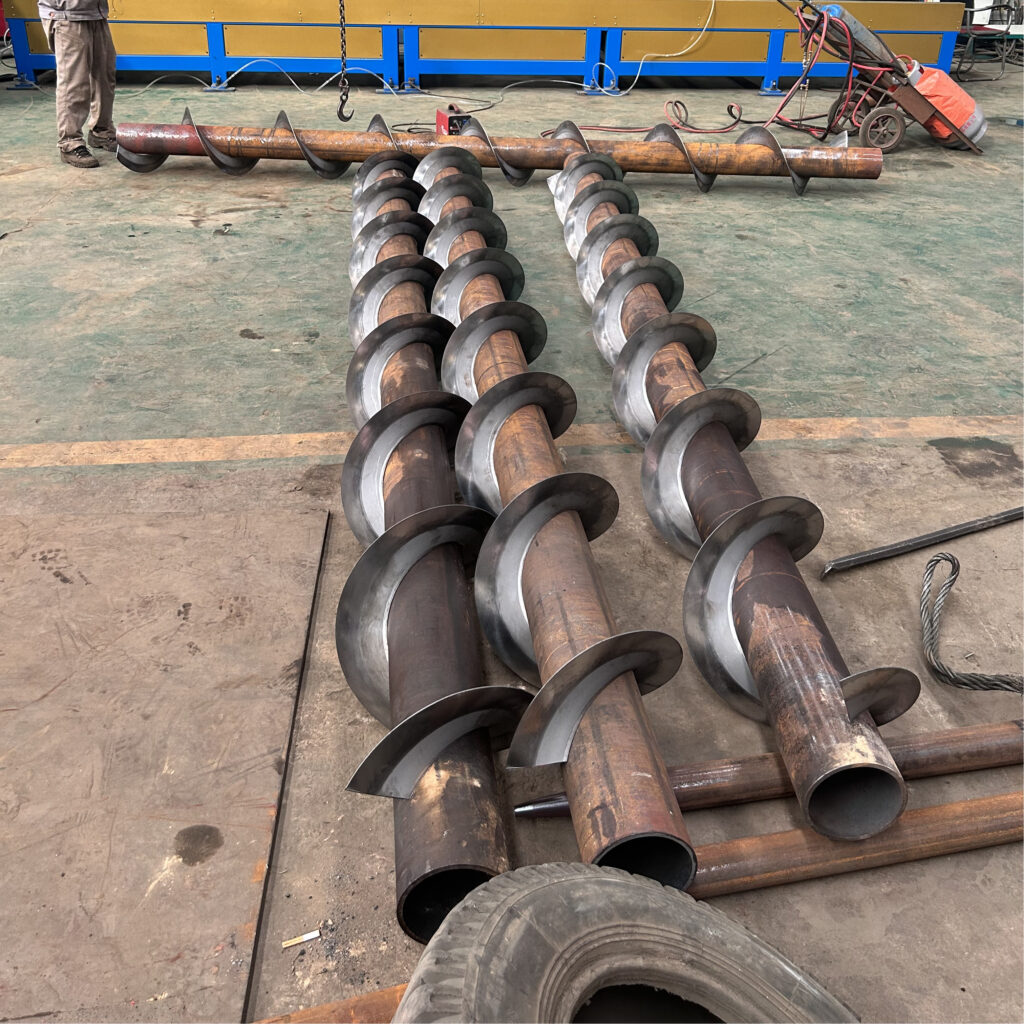
The advantages of an auger flight welding machine are numerous and significant, contributing to enhanced efficiency, precision, and reliability in the fabrication process. Some key advantages include:
1. Precision Welding: Auger flight welding machines ensure precise and consistent welding of flight segments onto pipes, minimizing the risk of misalignment or structural weaknesses. This precision results in higher quality finished products with uniformity in dimensions and welding integrity.
2. Increased Productivity: By automating the welding process, these machines significantly increase productivity compared to manual welding methods. They can weld auger flights onto pipes at a faster rate while maintaining high quality, allowing for higher production output within a shorter timeframe.
3. Cost Efficiency: While initial investment in auger flight welding machines may be higher, they offer long-term cost savings through reduced labor costs and increased production efficiency. The automation reduces the need for manual labor, leading to lower labor expenses over time.
4. Versatility: Auger flight welding machines are versatile and can accommodate various pipe diameters and flight sizes. This versatility allows manufacturers to produce a wide range of auger assemblies to meet different application requirements without the need for significant retooling or adjustments.
5. Consistency and Quality Control: Automation ensures consistent welding parameters, resulting in uniform weld quality throughout the production process. This consistency minimizes the risk of defects and ensures that each welded assembly meets the required standards and specifications.
6. Improved Safety: By automating the welding process, auger flight welding machines reduce the need for manual handling of hot welding equipment and materials, thereby enhancing workplace safety and reducing the risk of injuries associated with manual welding operations.
7. Enhanced Reliability: Welds produced by auger flight welding machines are typically of high quality and integrity, resulting in more reliable auger assemblies. This reliability is crucial in applications where failure of welded components can lead to costly downtime or safety hazards.
Overall, the advantages of auger flight welding machines make them indispensable tools for manufacturers seeking to optimize their production processes, improve product quality, and remain competitive in the industry.